In the oil and gas industry, HVAC (heating, ventilation, and air conditioning) systems play a crucial role in ensuring stable and safe operational conditions. However, there are several common problems that can affect the performance and efficiency of these systems, leading to additional costs and jeopardizing the safety of operations. By recognizing and avoiding these issues, you can ensure a safer and more profitable work environment.
In this article, we will explore the most frequent problems that affect HVAC systems in oil and gas plants and how to prevent them to ensure continuous and efficient operation.
1. Ventilation failures in critical areas
One of the most common issues in oil and gas facilities is the lack of proper ventilation in critical areas. In zones where hydrocarbons are processed, it is vital to maintain constant air circulation to prevent the accumulation of dangerous gases.
Prevention:
- Ensure that the ventilation systems are suitable for the conditions of the plant.
- Implement regular maintenance to clean ducts and avoid blockages.
- Use gas monitoring sensors to detect potential leaks before they become a danger.
2. Oversized or undersized HVAC systems
Having an HVAC system that does not properly match the needs of the plant can cause energy efficiency issues and high operational costs. An oversized or undersized system can result in unnecessary energy consumption or insufficient capacity to maintain stable temperatures.
Prevention:
- Perform an accurate calculation of the thermal load in each operational area.
- Ensure that the HVAC provider conducts a detailed analysis of the environmental conditions before installing the system.
- Perform preventive maintenance adjustments to ensure the system works correctly and avoid unnecessary wear on its components.
3. Corrosion and wear of components
Oil and gas plants are exposed to aggressive chemicals and corrosive vapors. If HVAC system components are not designed with resistant materials, corrosion can quickly affect the efficiency and lifespan of the equipment.
Prevention:
- Use corrosion-resistant materials, such as stainless steel for ducts and filters.
- Consider using anti-corrosive coatings in exposed areas.
- Conduct periodic inspections of systems to detect signs of corrosion before they cause major failures.
4. Lack of adequate preventive maintenance
One of the biggest mistakes you can make is not performing regular preventive maintenance. The accumulation of dirt, debris, or unattended minor failures can escalate into larger problems that affect operations.
Prevention:
- Establish a preventive maintenance plan that includes cleaning and reviewing key components like filters, ducts, and fans.
- Implement remote monitoring to detect issues in a timely manner.
- Train maintenance personnel on best practices and the importance of keeping the HVAC system in optimal condition.
5. Leaks in refrigeration systems
Leaks in refrigeration systems can lead to a drop in energy efficiency and, in the worst-case scenario, system failures. This is especially critical in environments where temperature control is vital for safety and production.
Prevention:
- Regularly inspect refrigeration systems for potential leaks.
- Use high-quality components that withstand wear from continuous use.
- Replace damaged parts immediately to prevent the problem from worsening.
6. Indoor air quality issues
Air quality is critical in work areas where hydrocarbons are processed. The accumulation of particles or toxic gases can pose a serious risk to the health of workers and operational efficiency.
Prevention:
- Ensure that the HVAC system is equipped with high-capacity industrial filters that capture particles and contaminants.
- Keep ventilation systems running properly to ensure a continuous flow of fresh air.
- Conduct periodic air quality tests and adjust the system as needed.
7. Temperature and humidity imbalances
In the oil and gas industry, precise control of temperature and humidity is vital to keep processes running smoothly. An imbalance in these parameters can affect productivity and plant safety.
Prevention:
- Install intelligent controllers and high-precision sensors to monitor and adjust temperature and humidity in real time.
- Perform maintenance adjustments to ensure that thermostats and sensors are functioning properly.
- Ensure that the HVAC system can maintain stable conditions year-round, regardless of fluctuations in outside climate.
8. Poor performance due to technological obsolescence
Technology in HVAC systems is advancing rapidly. If a plant continues using outdated or inefficient equipment, it may be missing out on opportunities to optimize performance and reduce operational costs.
Prevention:
- Invest in advanced technology that improves energy efficiency and temperature control.
- Conduct periodic performance evaluations of the system to identify areas for improvement.
- Consider updating obsolete components or implementing automation systems to improve efficiency.
What to do to avoid these common problems in the oil and gas industry?
HVAC systems are essential for maintaining stable and safe operational conditions in the oil and gas industry. However, if common problems are not addressed, costly issues may arise, jeopardizing both safety and efficiency.
To avoid these problems, it is key to perform proper maintenance, select the right materials, and adapt the system to the specific conditions of the plant. Additionally, investing in advanced technology can optimize performance, reduce energy consumption, and ensure a safer work environment.
At Doctor Frío A/C and Heating, we specialize in HVAC systems for the oil and gas industry. We offer customized solutions that ensure efficiency, safety, and regulatory compliance. Contact us today to learn how we can help you avoid these problems and optimize your operations’ performance.
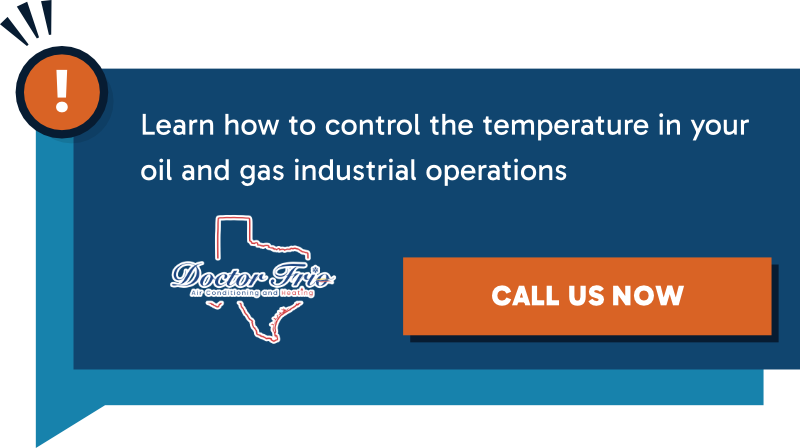